VAC-CON Florida Lighting
50%
48%
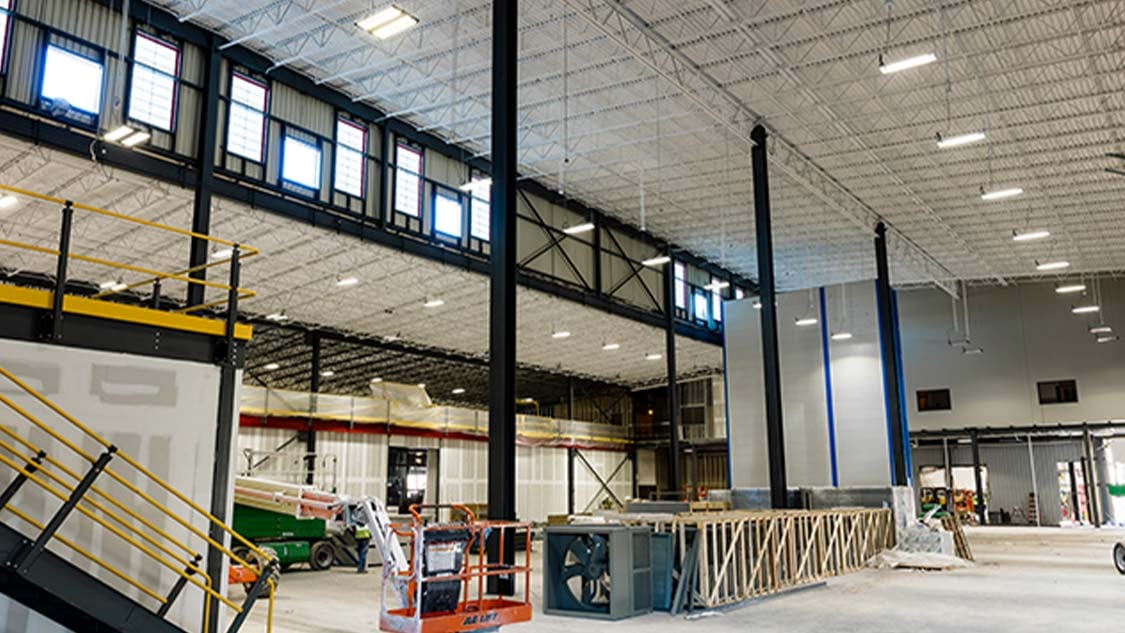
Since 1986, Vac-Con, Inc. has manufactured more than 7,000 custom-built, truck-mounted machines, including sewer vacuums and hydro excavators, to serve the public and private environmental markets worldwide, and now employs nearly 300 people at its single location in Green Cove Springs, Florida. Vac-Con, Inc. is a subsidiary of Holden Industries, Inc. of Deerfield, IL, and is 100% employee owned.
Lighting is not a sexy subject, but it hits bottom line costs. Good quality lighting improves people’s attitudes and how they approach work in a well-lit space. There is nobody who doesn’t like the Orion lighting.
Bill Barnes, Continuous Improvement Manager
Challenge
Vac-Con, Inc. faced a challenge common to many manufacturing facilities in multiple buildings on their campus. The complex lighting system, varying from metal halide to sodium vapor to fluorescent, had become a burden on the company, requiring significant investments in terms of technical knowledge, warehouse space, and capital spending to light their facilities. “Lighting is a part of our continuous improvement efforts, a strategic initiative launched in 2006 to replace old, latent technology that is energy consuming and wasting dollars that the business can use in a better format. Across our 17-acre site, those lighting dollars add up,” said Bill Barnes, Continuous Improvement Manager at Vac-Con.
- Performance – their existing 2×4 3-lamp T8 fluorescent lights were flickering and providing a poor quality of light that was too yellow for their needs.
- Operating costs – US Toy faced increasing electric rates and lamp replacement costs while their local utility began phasing out incentives for fluorescent lamps.
- Maintenance – staff spent a significant amount of time replacing burnt-out lamps yet the size of the overall maintenance team was being reduced.
“We have every kind of lighting that existed and from a facility management standpoint, we had to be able to fix every kind that existed. We needed to have the technical details and the on-hand, ready spare lamps to make that possible. Those dollars were not well spent sitting on shelves as replacements. From business process to physical processes, it was a huge administrative burden to have to find those parts,” said Barnes. Prior to the lighting upgrade, Vac-Con found that their poor lighting was causing them to miss flaws in their products during production, which led to more time and resources being spent on product re-work, rather than on new business.
Vac-Con’s multiple light systems also created work priority issues for the maintenance teams, who had to choose whether to spend time replacing burnt out lights or providing maintenance on the machinery. In addition, OSHA compliance required that Vac-Con document each lamp that comes into the facility and when each lamp was removed from a fixture, maintain receipts for every lamp in their inventory, and properly recycle lamps within a given timeframe or face fines.
We have every kind of lighting that existed and from a facility management standpoint, we had to be able to fix every kind that existed. We needed to have the technical details and the on hand, ready spare lamps to make that possible. Those dollars were not well spent sitting on shelves as replacements.
Bill Barnes, Continuous Improvement Manager
Solution
Over the last ten years, Vac-Con implemented higher efficiency interior fluorescent lighting fixtures from Orion to replace the mixture of sodium vapor and metal halide. The company found further improvement using inductive fluorescent fixtures provided by Orion to replace their aging metal halide exterior fixtures across the 17-acre campus. “We selected Orion because they are the subject matter experts in energy-efficient retrofit lighting, particularly in demanding environments. Together we engaged in assessing our power usage and the wide array of divergent lighting types in use at our facility,” said Bill Barnes, Six Sigma Black Belt and Continuous Improvement Manager at Vac-Con. “Orion helped us meet our energy reduction goals as we have incrementally engaged in continuous improvement projects by both standardizing our installed lighting types and in reducing our power footprint.”
In fact in many places, Vac-Con replaced previously installed Orion fluorescent technology with both LED High bay products in many of Vac-Con’s existing manufacturing spaces.
When the company decided to move forward on a major new construction project last year, it again turned to Orion to provide the LED lighting for the 60,000 square foot expansion that would increase its production capacity by 15 percent. For the project, Vac-Con chose Orion’s High Bay products because they met Vac-Con’s performance, efficiency and construction timelines. “For this new construction project, we returned to Orion because they got us the light levels and energy efficiency we needed, and in the timeline we required. It’s about getting the best value, and Orion has always been there to support us,” said Barnes.
By simply turning off the power to the luminaire, internal teams can use quick attachments to easily switch out aisle illuminators and modular power packs for driver replacement.
![]() |
![]() |
Result
“Vac-Con experienced greater than 48% energy demand reduction through both of these evolutions, and the current implementation of Orion LED technology furthers these ongoing energy savings efforts,” continued Barnes. “Our partnership with a dedicated and tireless vendor continues to pay forward as we complete our plant expansion project currently underway. Real project data makes lighting savings more beneficial and we’ve been able to think more strategically about lighting by providing measurable results with Orion.”
In addition to a nearly 50% increase in light levels, the Vac-Con project also shows that the benefits of a lighting retrofit cannot be measured in energy savings alone. Since upgrading to Orion’s LED fixtures, Vac-Con surveyed their employees who report they are able to pay better attention to their work and more cognizant of errors. The lighting led to quality and productivity improvements in the work they do and reduced the amount of re-work projects that Vac-Con must undertake. “Lighting is not a sexy subject, but it hits bottom line costs. Good quality lighting improves people’s attitudes and how they approach work in a well-lit space. There is nobody who doesn’t like the Orion lighting,” said Barnes.
The Orion LED lighting design not only met the operational and performance needs of the Vac-Con team and their varied facilities, but also allowed Vac-Con to standardize so as to significantly reduce their lighting inventory, waste stream, and maintenance at the same time. Barnes said, “Lots of people sell lights, but can you get me the light levels and energy savings I need and can you get it to me on time? I do my homework, and buy from the guy who gives me the best value, and that’s not always the lowest price. We return to Orion because of what they have taught us about lighting, because they are subject matter experts, and are always there to support us.”
![]() |
![]() |
![]() |
![]() |
![]() |
![]() |
![]() |
![]() |