What to Know About LED Lighting for Manufacturing Facilities — Part 1
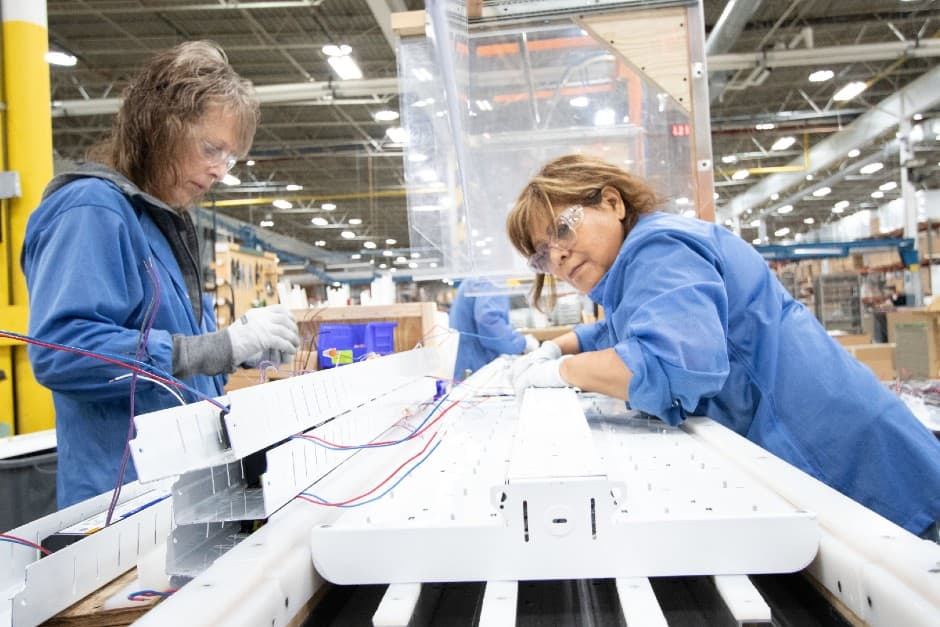
No two manufacturing facilities are alike – each is a unique environment with complex and often nuanced operational needs. Yet they all share one goal: to maintain optimum uptime and productivity.
Without the proper lighting, neither can be achieved.
That’s why best-in-class manufacturing organizations are upgrading their facilities with LED fixtures. These cost-effective, high-performance lighting options have been shown to improve productivity, enhance safety, reduce your carbon footprint, and more.
If you’re considering optimizing your facility with LED lighting, we’ll help you understand the key steps in the process in our 2-part blog series. This post, Part 1, outlines the preparations necessary before a lighting retrofit; in Part 2 (upcoming), we’ll review the steps involved in choosing the best fixtures for your facility and working environment.
Understand the Goal
Most every decision you make associated with your new lighting will hinge on “the why.” Be clear about the motivation for change — is it a desire to lower energy or other operating costs? Support sustainability initiatives? Comply with OSHA or other regulations? Improve safety?
Understanding what’s driving the project gives you and your lighting partner a foundation on which to build the most effective solution, both for today and for the future.
Commit a Budget
An LED retrofit that improves your operational efficiency and productivity is rarely “cheap,” but is an investment that pays for itself in a relatively short time. And, because LEDs lead to significant energy savings, there are a number of rebates available designed to encourage their use and make them even more affordable.
Orion offers an Energy-as-a-Service program, giving customers access to premier lenders at preferred rates in order to move forward with retrofit projects without the need to utilize capital dollars. These lenders have customized terms and often allow for no cash down. If you’re interested, reach out to our team.
Review Current Equipment
Installing new lighting equipment doesn’t always mean tearing out what’s already in place.
Some of your existing lighting equipment or infrastructure may still be appropriate for new fixtures, or might simply require adjustments. Depending on the age, condition, and performance of your existing equipment, however, it might be most practical (or even necessary) to remove it.
Orion begins each engagement by doing a comprehensive facility audit to review what you have today and determine what’s usable, what needs to be replaced, and what new fixture and lighting control options will align best with your needs. The audit is detailed and includes (but is not limited to) the review of:
- Room environments (temperature, humidity, vibration, etc.)
- Ceiling height and structure
- Fixture hours of operation
- Fixture height, type, quantity, length/width, and spacing
- Fixture controls
- Emergency battery backup needs
- Lamp type, size, and wattage
- Existing ballast type
- Voltage
- Lens types and/or light distribution requirements
- Foot candle levels
- Power needs
Request a free facility audit from Orion!
Identify the Least Disruptive Installation Schedule
Installing new lighting equipment in a manufacturing facility can be a big undertaking, and one that challenges facility managers and workers to stick to a normal schedule of operations.
Our installation teams are acutely aware of the importance of maintaining the highest possible level of uptime. To that end, we’ll work with your team to identify the least disruptive times to install your new lighting.
Whether it’s Orion or another energy service company doing the installation, the work is made simple when we supply the products — because all packages are clearly labeled and matched to the exact location they’re going to for streamlined installation.
Related: How to Choose the Right Fixtures and Partner for an LED Retrofit
Part 2 Preview: LED Fixture Considerations
Once you’ve made these preparations and your facility ready for new lights, it will be time to select the most ideal fixtures. What features must your lights have? Part 2 will highlight such factors as light levels, chemical resistance, surge protection, and more.
Read Part 2: What To Know About LED Lighting for Manufacturing Facilities
Ready to Upgrade?
Think you’re ready for new, energy-efficient LED lighting and all it has to offer? We’re happy to discuss how your organization can benefit. Click the link below to get the conversation started!
Subscribe to Energy Insights
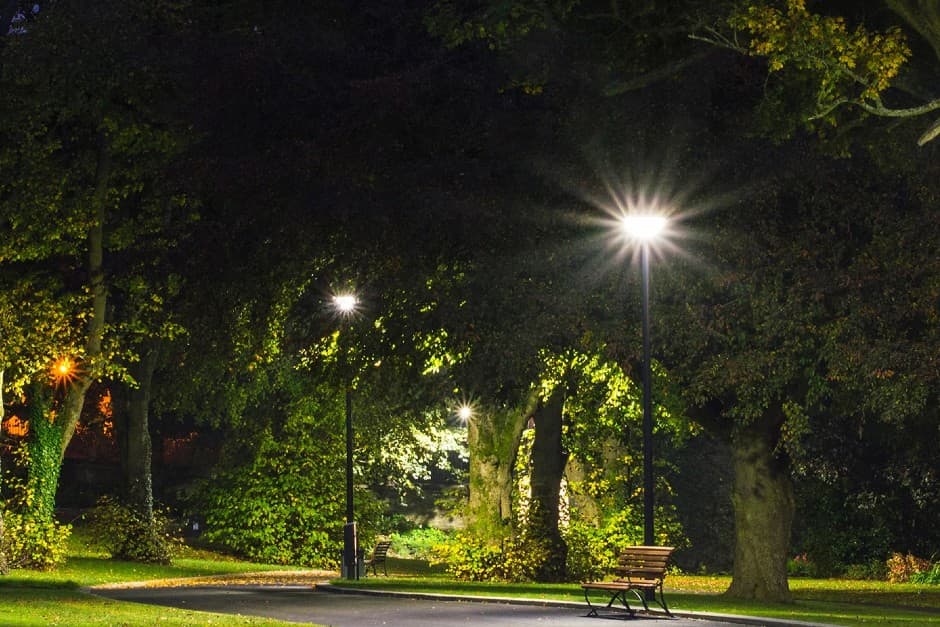
5 Considerations When Selecting Commercial Outdoor LED Lighting
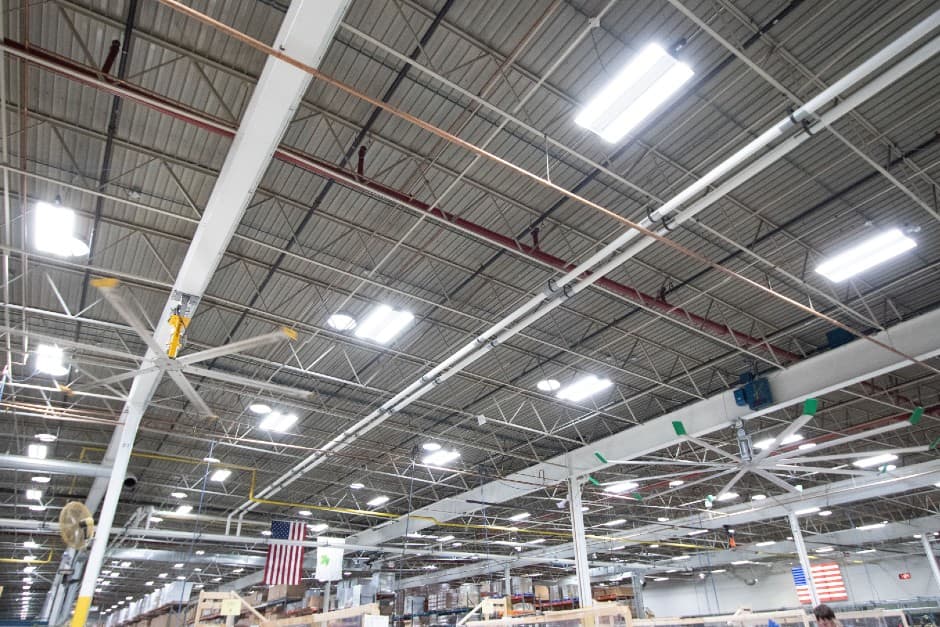
5 Commonly Asked Questions About Commercial LED Lighting
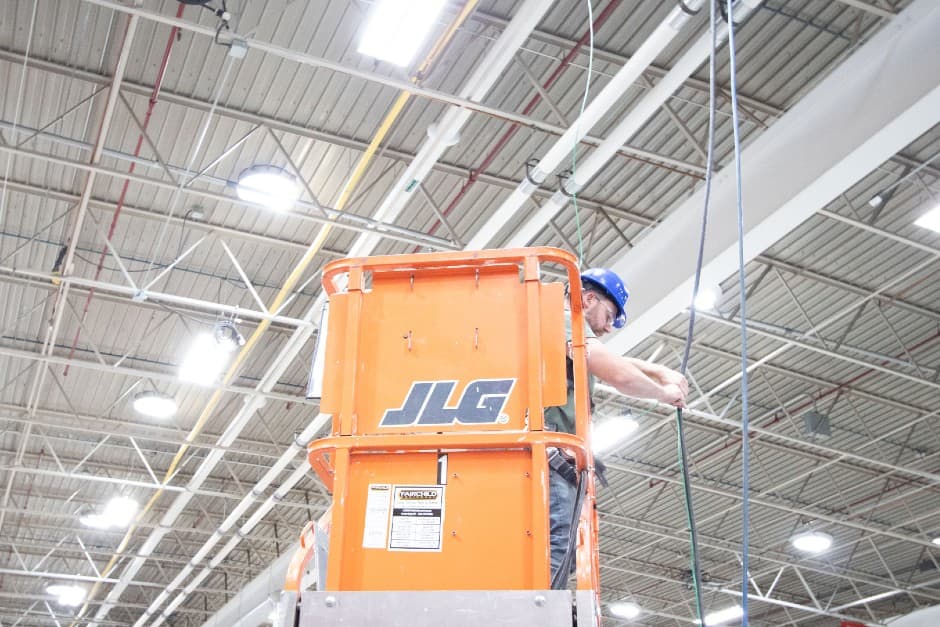