What To Know About LED Lighting for Manufacturing Facilities — Part 2
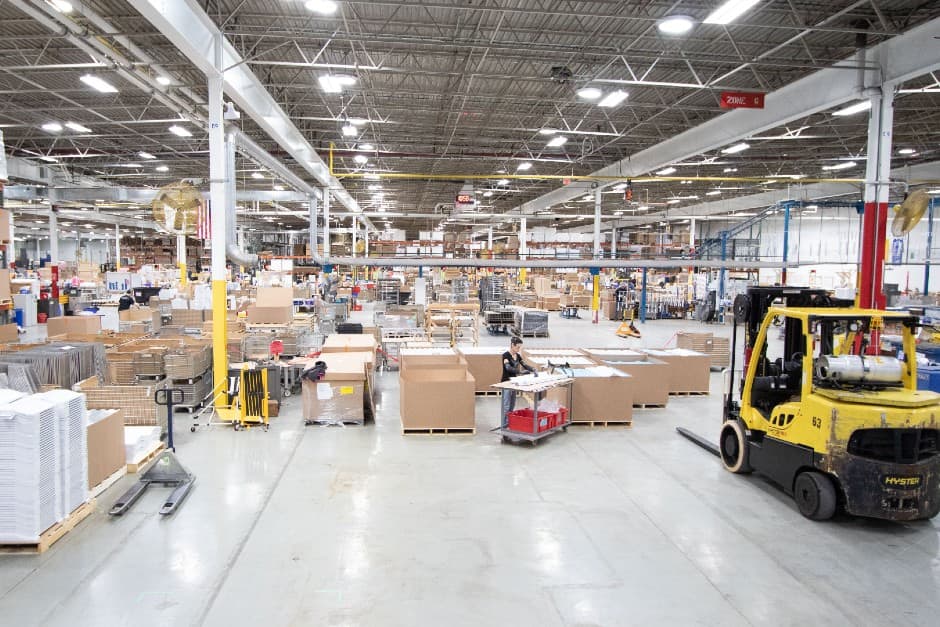
This is the second installment of a two-part article. In Part 1, we outlined the preparations necessary before embarking on an industrial lighting retrofit. Part 2 is a look at features that need to be considered in order to ensure the proper levels of illumination, heat and cold resistance, chemical resistance, ambient operating temperature range, surge protection, and more.
LED Fixture Considerations and Compliance
IES Light Level
To help safeguard workers – and optimize their productivity – the Illuminating Engineering Society (IES) recommends a range of light levels (expressed in foot-candles, or FCs) for different industrial settings.
Your specific application will determine the exact foot-candle levels required. Keep in mind that local, federal, and business foot-candle requirements may differ based on zoning or on the tasks being performed in that area.
NOTE: The following selected foot-candle ranges represent the Illuminating Engineer Society's (IES) current illumination recommendations. Individual applications will determine exact foot-candle levels. Please refer to the latest most current IES Lighting Handbook 10th Edition for a more detailed evaluation.
Interior Lighting
Application (Industrial) |
Horizontal Average (FC*)1,2 |
Maintained Horizontal Range (FC)3,2 |
Vertical Average (FC)1,2 |
Maintained Vertical Range (FC)3,2 |
||||
---|---|---|---|---|---|---|---|---|
Assembly & Inspection (Simple) Component Manufacture (Large Parts) |
Horizontal Average (FC*)1,2 | 30 | Maintained Horizontal Range (FC)3,2 | 15-60 | Vertical Average (FC)1,2 | 30 | Maintained Vertical Range (FC)3,2 | 15-60 |
Component Manufacture (Medium Parts) |
Horizontal Average (FC*)1,2 | 50 | Maintained Horizontal Range (FC)3,2 | 25-100 | Vertical Average (FC)1,2 | 50 | Maintained Vertical Range (FC)3,2 | 25-100 |
Assembly & Inspection (Difficult) Component Manufacture (Fine Parts) |
Horizontal Average (FC*)1,2 | 100 | Maintained Horizontal Range (FC)3,2 | 50-200 | Vertical Average (FC)1,2 | 100 | Maintained Vertical Range (FC)3,2 | 50-200 |
General Food Processing4 |
Horizontal Average (FC*)1,2 | 75 | Maintained Horizontal Range (FC)3,2 | 37.5-150 | Vertical Average (FC)1,2 | 20 | Maintained Vertical Range (FC)3,2 | 10-40 |
Exterior Lighting
Application5 |
Horizontal Average (FC)1,2 |
Maintained Horizontal Range (FC)3,2 |
Vertical Average (FC)1,2 |
Maintained Vertical Range (FC)3,2 |
||||
---|---|---|---|---|---|---|---|---|
Parking (Uncovered) Zone 3 (Urban) |
Horizontal Average (FC*)1,2 | 1.5 | Maintained Horizontal Range (FC)3,2 | 0.75-3 | Vertical Average (FC)1,2 | 0.8 | Maintained Vertical Range (FC)3,2 | 0.4-1.6 |
Parking (Uncovered) Zone 2 (Suburban) |
Horizontal Average (FC*)1,2 | 1 | Maintained Horizontal Range (FC)3,2 | 0.5-2 | Vertical Average (FC)1,2 | 0.6 | Maintained Vertical Range (FC)3,2 | 0.3-1.2 |
Parking (Covered) |
Horizontal Average (FC*)1,2 | 5 | Maintained Horizontal Range (FC)3,2 | - | Vertical Average (FC)1,2 | - | Maintained Vertical Range (FC)3,2 | - |
Safety (Building Exterior) |
Horizontal Average (FC*)1,2 | 1 | Maintained Horizontal Range (FC)3,2 | 0.5-2 | Vertical Average (FC)1,2 | - | Vertical Average (FC)1,2 | - |
* Foot-candles
1At least half of the users/occupants are in the age range of 25-65 years old.
2The horizontal measurement is known as the horizontal illuminance and is the amount of light that lands on a horizontal surface, such as a tabletop. The vertical measurement is known as the vertical illuminance and is the amount of light that lands on a vertical surface, such as a wall.
3Ranges are based on situations in which at least half of users are < 25 years of age (low value) and > 65 years of age (high value).
4The light levels for specific tasks may vary per type of food processing. For more information consult IES Handbook 10th Edition Chapter 30.
5If a section has been left blank, it means IES has not made a recommendation. Please reference NEC, local, and state codes to determine horizontal and vertical foot-candles.
OSHA Compliance
While the IES has outlined recommendations, OSHA has developed requirements specific to lighting in industrial settings, and failure to comply could result in fines.
According to OSHA, generalized lighting should be evenly distributed throughout the workplace, without gaps, so that workers can see and navigate without straining their eyes. What does it take to satisfy that requirement? OSHA has set the candle-feet of light (this term refers to the illuminance of one square foot of surface from a uniform source of light) required for the work done in various areas within a manufacturing facility:
- First-aid stations, offices, and infirmaries: 30 foot-candles
- General construction plants and shops: 10 foot-candles
- General construction areas: 5 foot-candles
- Warehouses, walkways, corridors, exits, and other indoor spaces: 5 foot-candles
- Concrete placement, waste areas, loading platforms, active storage areas, field maintenance areas, refueling areas, and excavation sites: 3 foot-candles
Racking & Light Distribution
Proper warehouse lighting is key to ensuring that the work performed in these areas is carried out safely and accurately. Warehouse workers read information on container tags and labels in order to sort, inspect, select, and stock products and shipments. Light fixtures in these areas need to be capable of illuminating the vertical surfaces of boxes and racks.
The spacing of a facility’s high bay fixtures is important, too. If the space between fixtures is too great, illumination will “drop off” in spots; if it’s too tight, glare could become a problem near the tops of racks. IESNA recommends that rack areas within warehouses target illuminance of between 20 and 50 vertical foot-candles.3 The specific illumination requirements within that range will depend on a number of factors.
Color Rendering Index (CRI)
A fixture’s rating on the Color Rendering Index (CRI) is a measure of how naturally the light source reveals an object’s true colors when compared to a natural or standard light source. The CRI index goes from 0 to 100; at 0, all colors look the same, and at 100 you see the true colors of the object.
It’s important for workers in manufacturing environments to accurately see colors, as they’re often used to indicate specific hazards. Red, for example, is used to indicate fire protection equipment and hazard areas; orange indicates dangerous machine and equipment parts; and yellow indicates physical hazards and materials that are potentially hazardous to life and property.1 Equipment controls and diagrams are often color-coded, as well.
Heat and Cold Resistance
Heavy machinery in manufacturing facilities tends to generate a significant amount of heat, and heat can compromise the performance of electronic equipment. In these environments, the ideal LED fixture heat tolerance is between 50°C and 55°C (122°F-131°F). LEDs in environments where the temperatures are higher than this may still work, but they will likely have shorter lifespans.
Similarly, cold storage and freezer environments require lighting fixtures that can withstand the facility’s ambient temperatures. Orion offers certified high bay fixtures specifically designed to operate in a temperature range from -40°C to 50°C (-40°F to 122°F.)
How is the lifespan of an LED fixture calculated?
L70 is an LED lifetime measurement criteria developed by IESNA (Illuminating Engineering Society of North America) to evaluate the useful lifetime of an LED fixture in terms of the expected number of operating hours until the light output has diminished to 70% of initial levels. If your fixture has a stated lifespan of 25,000 hours, for example, that means that at 25,000 hours the fixture will be producing 70% of the amount of light it produced on its first day in use. (The fixture will not stop working after its stated lifetime has been reached, but will continue to produce less light.)
Chemical Resistance
Chemicals are often employed in manufacturing processes to wash or sterilize surfaces, and lighting in areas where they’re used must be able to withstand exposure to them. Material Safety Data Sheets (MSDS) will inform you about chemicals in use that could affect LEDs’ performance or the materials used in their structures (plastic housings, power connection supply, and lenses).
Power Surge Protection
Surges of power, also called transients, are brief overvoltage spikes or disturbances of a power waveform that can damage or destroy electronic equipment. Transients can reach amplitudes of tens of thousands of volts – scenarios that have the potential to completely shut down operations.2
You’ll want to install LED fixtures that have a built-in 6kV standard of protection against uneven use of power or sudden surges. For added protection, Orion often adds transient voltage surge suppressor (TVSS) systems directly to lighting panels to address any transient voltage before it reaches the light fixture. Orion also offers additional surge protection as an option on our fixtures (20kV).
Energy Savings
Facility directors know that adjusting lighting based on an area’s usage and time of day is an effective way to decrease energy costs. Many use controls to dim lights to acceptable levels when workers aren’t present (and turn back up when motion is detected), and to shut off automatically when the plant isn’t operating.
Orion offers a range of controls, from simple sensors to those with sophisticated networking capabilities that enable users to connect their facilities’ lighting systems and control them remotely.
We’re true partners with our customers, working together to determine the most appropriate lighting for their needs, and following up with attentive service and support. If you’re considering LED fixtures for your facility, we’d love to demonstrate the value we’ll bring to your project. Reach out today!
SOURCES
Subscribe to Energy Insights
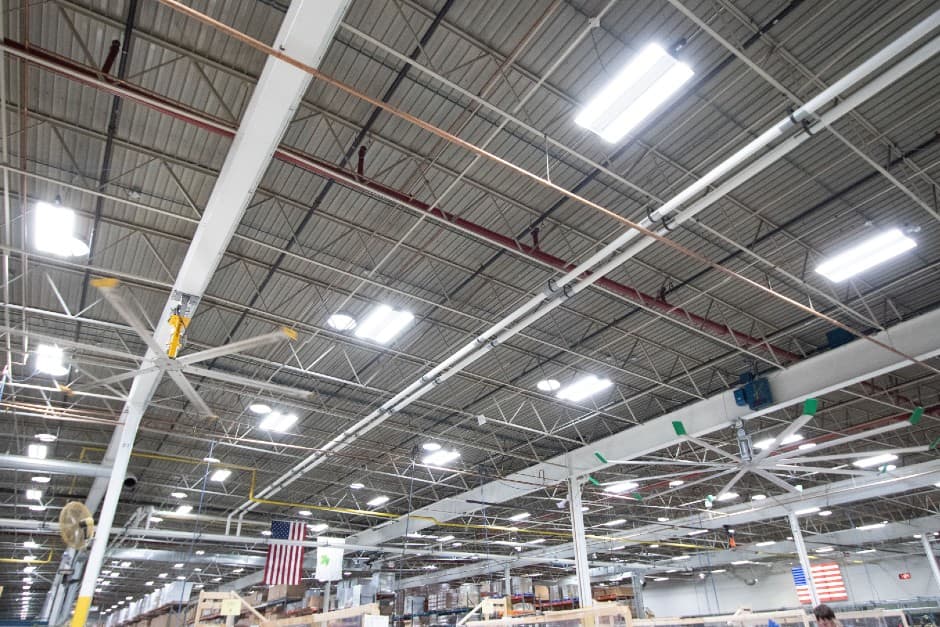
5 Commonly Asked Questions About Commercial LED Lighting
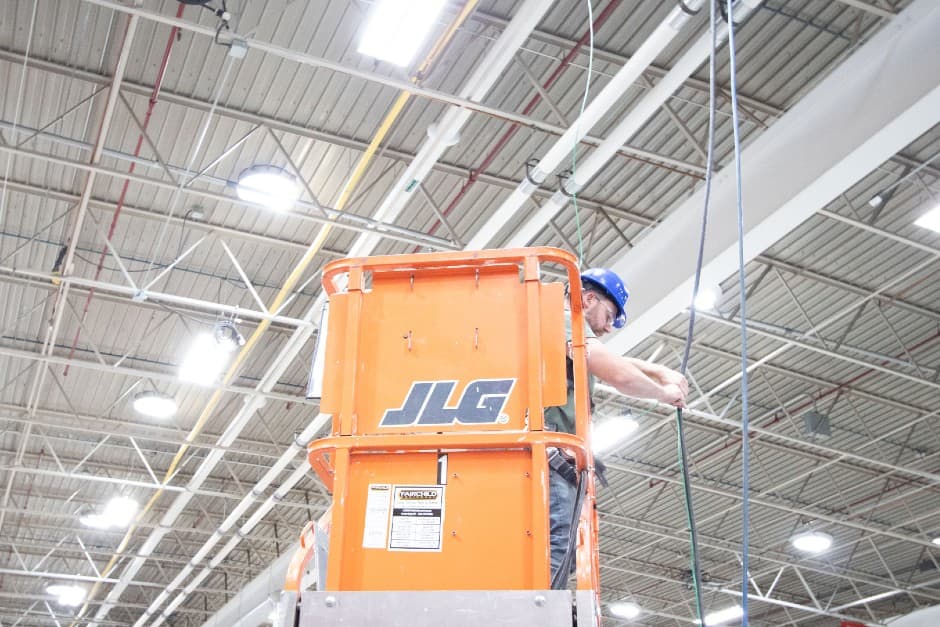
6 LED Retrofit Services You Should Expect From Your Lighting Provider
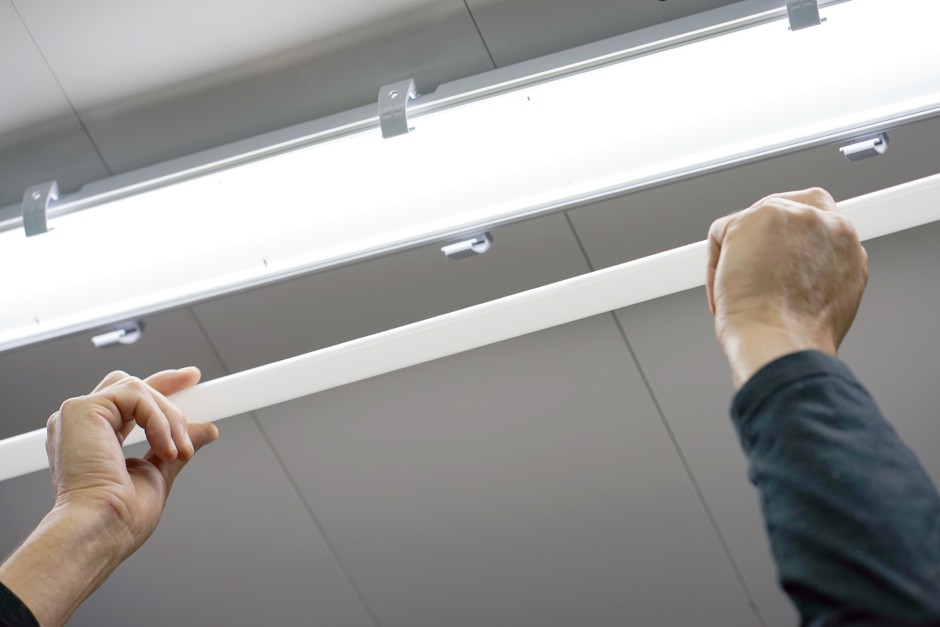